PRODUCTS Categories
CONTACT US
- Phone:
- 86 17344894490
- Tel:
- 86 17344894490
- Email:
- business@signialuminium.com
- Add:
- Zhengzhou, Henan, China.
Industry News
Influence the quality of clear anodized aluminum film
Time :2017-11-16
Several major factors that influence the quality of clear anodized aluminum film
1. The current density: within a certain limit, the current density increases, the membrane growth rate increases, the oxidation time is shortened, the membrane is more porous, and the hardness and wear resistance are higher.If the current density is too high, the heat of the parts will be overheated and the temperature of the local solution will rise, the dissolution rate of the membrane will be increased, and the possibility of burning the parts will be burned.The current density is too low, and the film growth rate is slow, but the film is dense, and the hardness and wear resistance are lower.
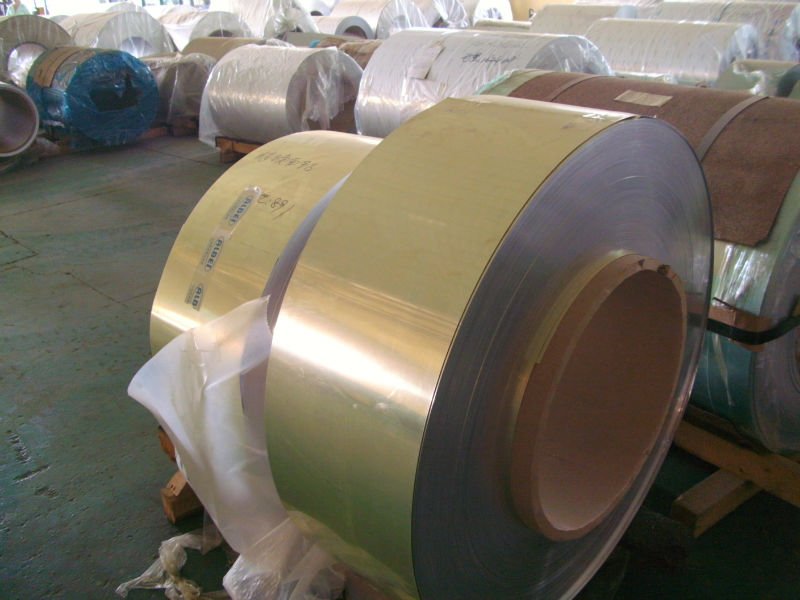
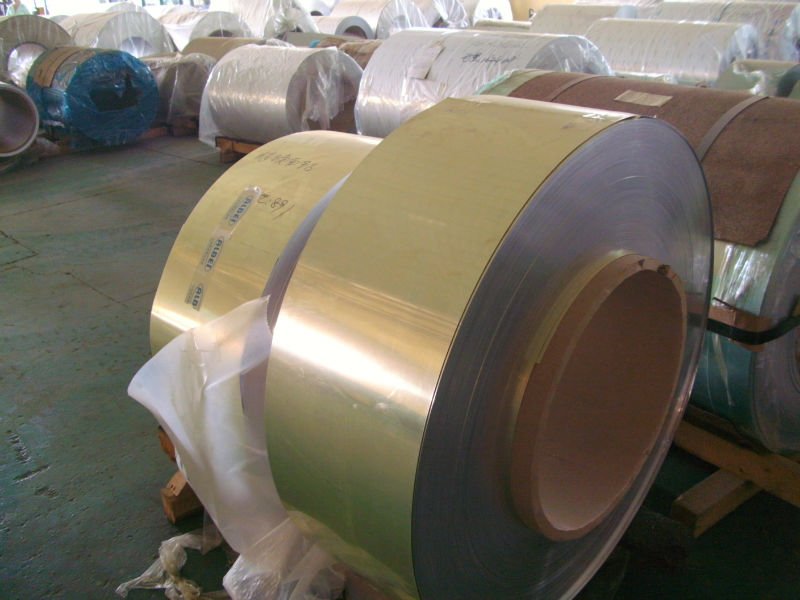
Clear anodized aluminum, which is used for protection, decoration and pure decorative processing, USES the upper limit of the allowable concentration, which is 20% concentration of sulfuric acid for electrolyte. 【clear anodized aluminum】
2. Oxidation time: the choice of oxidation time depends on the concentration of the electrolyte, the temperature, the anode current density and the required film thickness.Under the same conditions, when the current density is constant, the growth rate of the membrane is proportional to the oxidation time.But when the film growth to a certain thickness, due to the membrane resistance increases, affect the conductive ability, and because the temperature rise, the dissolution rate of membrane increases, so the film growth rate will decrease gradually, until the last no longer increases.
3. Concentration of sulfuric acid: usually 15% - 20%.Concentration increases, the dissolution rate of membrane increased, the growth speed of membrane, membrane of high porosity, adsorption capacity is strong, flexible, good dyeing (easy to dye the dark), but the hardness, wear resistance of slightly;And the concentration of sulfuric acid was reduced, and the growth rate of the oxide film was accelerated, the pores of the membrane were low, the hardness was high and the wear resistance was good. 【clear anodized aluminum】
4. Electrolyte temperature: the electrolyte temperature has a great influence on the quality of the oxide film.Temperature rise, film dissolution rate increases, film thickness decreases.When the temperature is 22-30 ℃, the resulting film is soft, good adsorption ability, but wearability is poor;When the temperature is greater than 30 ℃, the film became loose and uneven, and sometimes even discontinuous, and the hardness is low, thus lost the use value;When the temperature is between 10-20 ℃, the generated porous oxide film, adsorption ability, and full of elasticity, suitable for dyeing, but the film hardness is low, poor wear resistance;When the temperature is below 10 ℃, the increase of the thickness of the oxide film, high hardness, good wear resistance, but low porosity.Therefore, the temperature of the electrolyte must be controlled strictly.In order to make a thick and hard oxide film, the operating temperature must be reduced. In the process of oxidation, the compressed air should be stirred and the lower temperature is used. 【clear anodized aluminum】
5. Mixing and moving: can promote the electrolyte convection, strengthen the cooling effect, ensure the uniformity of the temperature of the solution, and not cause the degradation of the oxide film due to the local heating of the metal.
6. Impurities in the electrolyte: the possible impurities in the electrolyte used in the oxidation of aluminum anodes are Cl - inverse, F inverse, NO3 inverse, Cu2+,Al3+,Fe2+ etc.Among them, Cl - inverse, F - inverse, NO3 - induced porosity increase, surface roughness and porosity.If its content exceeds the limit value, it may even cause corrosion perforation of the making parts (Cl shall be less than 0.05g/L, and F inverse should be less than 0.01 g/L);When the Al3+ content exceeds a certain value in the electrolyte, the surface of the workpiece often appears white or speckled white, and the adsorption performance of the film decreases, and the dyeing difficulty (Al3 + should be less than 20g/L).When Cu2+ content reaches 0.02 g/L, dark streaks or black spots appear on the oxide film;Si2+ is often suspended in the electrolyte, causing the electrolyte to be microturbid and adsorbed on the membrane with a brown powder. 【clear anodized aluminum】
7. All landowners aluminum alloy components: in general, the quality of the other elements make the film of aluminum metal drops, and didn't get the pure aluminium oxide layer with the thickness, hardness too low, different composition of aluminum alloy, in the anodic oxidation process should pay attention to not with groove.