PRODUCTS Categories
CONTACT US
- Phone:
- 86 17344894490
- Tel:
- 86 17344894490
- Email:
- business@signialuminium.com
- Add:
- Zhengzhou, Henan, China.
Company News
5052 anodized aluminum coil strip
Time :2020-06-10
5052 anodized aluminum coil is the most widely used coil. This alloy has high strength, especially fatigue resistance, high plasticity and corrosion resistance, and cannot be strengthened by heat treatment. The plasticity is still good when it is hardened by semi-cold work. It has low plasticity during hardening, good corrosion resistance, good weldability, poor cutting performance and can be polished.
Aluminum-magnesium alloy also contains a small amount of manganese, chromium, beryllium, titanium and so on. Except for a small amount of solid solution, most of the manganese in the alloy forms MnAl6. The role of chromium in anodized aluminum coils is similar to that of manganese, improving the ability to resist stress corrosion cracking, increasing the strength of the base metal and the weld, and reducing the tendency of welding cracks, but its content generally does not exceed 0.35%.
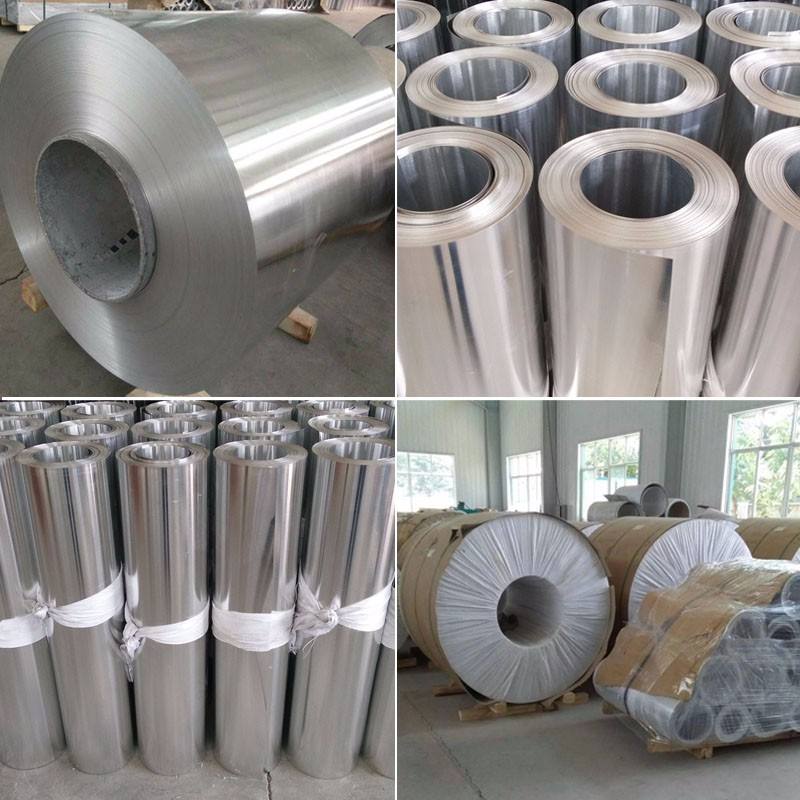
5052 Anodized aluminium roll introduction
The process of 5052 anodised aluminum coil strip is to use aluminum or aluminum alloy products as the anode, placed in an electrolyte solution for energization treatment, and the process of forming an aluminum oxide film on the surface by electrolysis is called anodization of aluminum and aluminum alloy. After the anodized aluminum roll is anodized, an aluminum oxide film can be formed on the surface of a few microns-a few hundred microns. Compared with the natural oxide film of aluminum alloy, its corrosion resistance, abrasion resistance and decoration are all significantly improved and improved.
The main purpose:
(1) Improve the wear resistance, corrosion resistance and weathering resistance of parts.
(2) The transparent film produced by oxidation can be made into various colored films by coloring.
(3) As a capacitor dielectric film.
(4) Improve the cohesion with organic coatings. Used as the bottom coat.
(5) As the bottom layer of electroplating and enamel.
(6) Other applications under development, such as solar energy absorption panels, ultra-high hard films, dry lubricating films, catalyst films, nanowires, and magnetic alloys deposited in porous films as memory elements.
Aluminum-magnesium alloy also contains a small amount of manganese, chromium, beryllium, titanium and so on. Except for a small amount of solid solution, most of the manganese in the alloy forms MnAl6. The role of chromium in anodized aluminum coils is similar to that of manganese, improving the ability to resist stress corrosion cracking, increasing the strength of the base metal and the weld, and reducing the tendency of welding cracks, but its content generally does not exceed 0.35%.
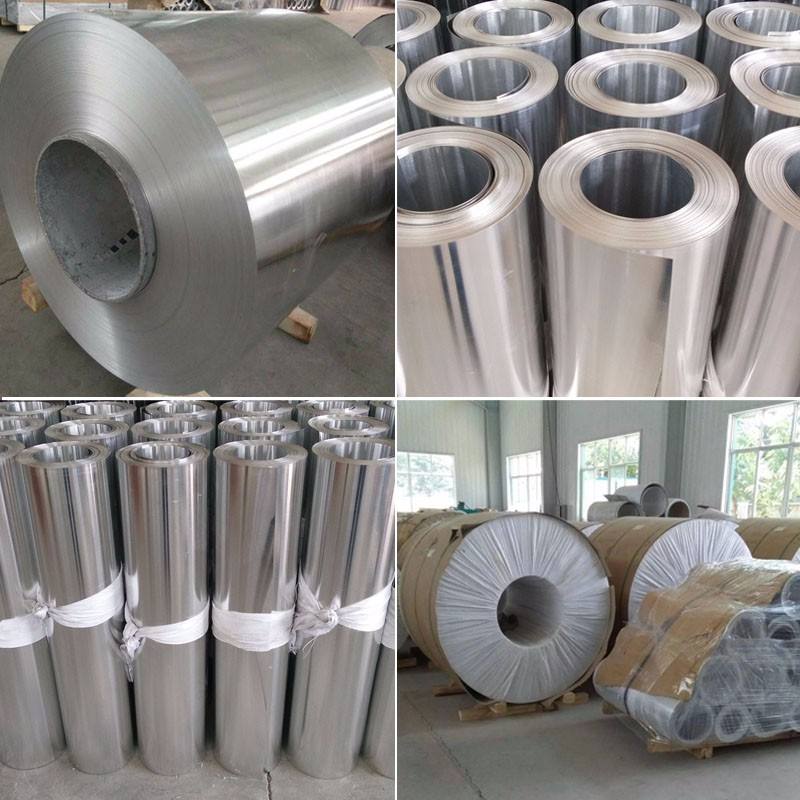
5052 Anodized aluminium roll introduction
The process of 5052 anodised aluminum coil strip is to use aluminum or aluminum alloy products as the anode, placed in an electrolyte solution for energization treatment, and the process of forming an aluminum oxide film on the surface by electrolysis is called anodization of aluminum and aluminum alloy. After the anodized aluminum roll is anodized, an aluminum oxide film can be formed on the surface of a few microns-a few hundred microns. Compared with the natural oxide film of aluminum alloy, its corrosion resistance, abrasion resistance and decoration are all significantly improved and improved.
The main purpose:
(1) Improve the wear resistance, corrosion resistance and weathering resistance of parts.
(2) The transparent film produced by oxidation can be made into various colored films by coloring.
(3) As a capacitor dielectric film.
(4) Improve the cohesion with organic coatings. Used as the bottom coat.
(5) As the bottom layer of electroplating and enamel.
(6) Other applications under development, such as solar energy absorption panels, ultra-high hard films, dry lubricating films, catalyst films, nanowires, and magnetic alloys deposited in porous films as memory elements.