PRODUCTS Categories
CONTACT US
- Phone:
- 86 17344894490
- Tel:
- 86 17344894490
- Email:
- business@signialuminium.com
- Add:
- Zhengzhou, Henan, China.
Company News
How to prevent darkening of aluminum anodized film
Time :2019-03-20
1. For different aluminum alloys, such as casting, calendering or mechanical forming or heat treatment welding, it is necessary to select a suitable pretreatment method according to the actual situation. For example, for the surface of a cast aluminum alloy, the non-machined surface should be sandblasted or shot blasted to remove the original oxide film, sticky sand, and the like. Aluminum alloys with high silicon content (especially cast aluminum) should be etched and activated by a mixed acid solution containing about 5% hydrofluoric acid to effectively maintain a good activated surface and ensure the quality of the anodised aluminium film. Aluminum alloys of different materials, bare aluminum and pure parts or aluminum and aluminum alloy parts with different sizes and specifications are generally not suitable for treatment in the same tank.
For the aluminum alloy assembly of lap joint, spot welding or riveting, for the aluminum alloy parts which are easy to be formed in the anodizing process of aluminum, it is generally not allowed to adopt the aluminum sulfate anodizing process from the viewpoint of quality.
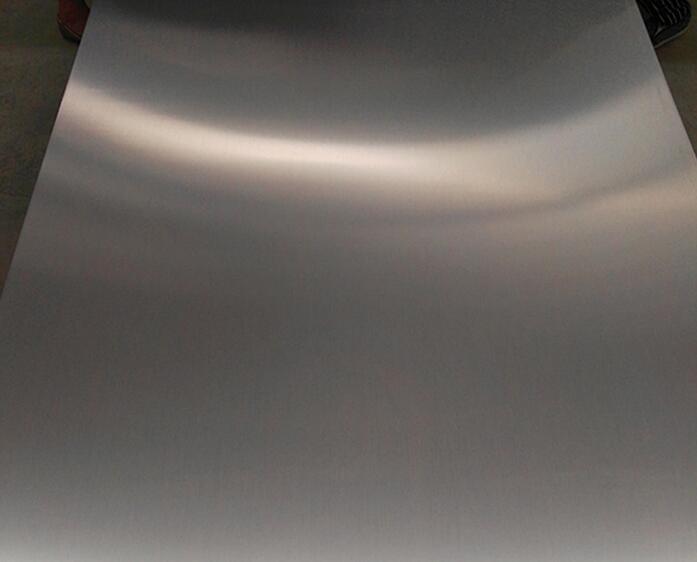
2. The material of the mounting fixture must ensure good electrical conductivity. Generally, a hard aluminum alloy rod is used, and the sheet should have certain elasticity and strength. The hook should be made of copper or copper alloy. Dedicated or general-purpose jigs that have been used, such as aluminum anodizing, should be used again, and the surface oxide film must be completely removed to ensure good contact. The fixture must ensure sufficient conductive contact area and minimize fixture marks. If the contact surface is too small, it will cause burnt aluminium anodized parts.
3. The temperature of the aluminum sulfate anodizing solution must be strictly controlled, and the optimum temperature range is 15 to 25 °C. Compressed air agitation is required during the anodizing process of aluminum sulfate, and a refrigeration unit should be provided. In the absence of a refrigerating device, adding 1.5% to 2.0% of tricarboxylic acid or carboxylic acid such as oxalic acid or lactic acid to the sulfuric acid electrolyte can make the aluminum anodizing solution temperature range exceed 35 ° C to avoid or reduce the aluminum anodised film. Loose or powdered.
4. The water quality used in the anodizing electrolyte of aluminum sulfate and the harmful impurities in the electrolyte must be strictly controlled. It is not suitable to use tap water for the preparation of aluminum sulfate anodizing solution, especially for turbid tap water containing Ca2+, Mg2+, SiO32- and Cl-. Under normal circumstances, when the concentration of Cl- in water reaches 25 mg/L, it will have a detrimental effect on the anodizing treatment of aluminum. Cl- (including other halogen elements) can destroy the formation of an oxide film, or even form an oxide film at all. Alumina sulfate anodizing should use demineralized water, deionized water or distilled water, Ccl-≤15mg/L in the electrolyte, and total minerals ≤50 mg/L.
In the aluminum anodizing process, the sulfuric acid solution will produce oily foam and suspended impurities, which should be regularly eliminated. Other harmful impurities commonly found in aluminum sulfate anodizing solutions are Cu2+, Fe3+, Al3+ and the like. If the impurity content exceeds the allowable content, harmful effects may occur, and the sulfuric acid solution may be partially or completely replaced to effectively ensure the anodization quality of the aluminum alloy sulfuric acid.
For the aluminum alloy assembly of lap joint, spot welding or riveting, for the aluminum alloy parts which are easy to be formed in the anodizing process of aluminum, it is generally not allowed to adopt the aluminum sulfate anodizing process from the viewpoint of quality.
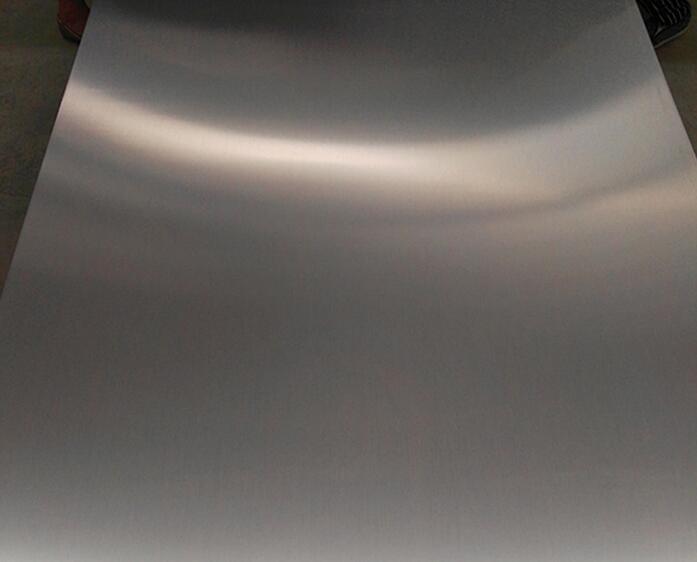
2. The material of the mounting fixture must ensure good electrical conductivity. Generally, a hard aluminum alloy rod is used, and the sheet should have certain elasticity and strength. The hook should be made of copper or copper alloy. Dedicated or general-purpose jigs that have been used, such as aluminum anodizing, should be used again, and the surface oxide film must be completely removed to ensure good contact. The fixture must ensure sufficient conductive contact area and minimize fixture marks. If the contact surface is too small, it will cause burnt aluminium anodized parts.
3. The temperature of the aluminum sulfate anodizing solution must be strictly controlled, and the optimum temperature range is 15 to 25 °C. Compressed air agitation is required during the anodizing process of aluminum sulfate, and a refrigeration unit should be provided. In the absence of a refrigerating device, adding 1.5% to 2.0% of tricarboxylic acid or carboxylic acid such as oxalic acid or lactic acid to the sulfuric acid electrolyte can make the aluminum anodizing solution temperature range exceed 35 ° C to avoid or reduce the aluminum anodised film. Loose or powdered.
4. The water quality used in the anodizing electrolyte of aluminum sulfate and the harmful impurities in the electrolyte must be strictly controlled. It is not suitable to use tap water for the preparation of aluminum sulfate anodizing solution, especially for turbid tap water containing Ca2+, Mg2+, SiO32- and Cl-. Under normal circumstances, when the concentration of Cl- in water reaches 25 mg/L, it will have a detrimental effect on the anodizing treatment of aluminum. Cl- (including other halogen elements) can destroy the formation of an oxide film, or even form an oxide film at all. Alumina sulfate anodizing should use demineralized water, deionized water or distilled water, Ccl-≤15mg/L in the electrolyte, and total minerals ≤50 mg/L.
In the aluminum anodizing process, the sulfuric acid solution will produce oily foam and suspended impurities, which should be regularly eliminated. Other harmful impurities commonly found in aluminum sulfate anodizing solutions are Cu2+, Fe3+, Al3+ and the like. If the impurity content exceeds the allowable content, harmful effects may occur, and the sulfuric acid solution may be partially or completely replaced to effectively ensure the anodization quality of the aluminum alloy sulfuric acid.